На предприятии ГК "Русская кожа" изготавливают высококлассную продукцию на максимально автоматизированном производстве
В 2022 году новый кожевенный завод в Заринске планирует выйти на 90% проектной мощности. Уже в текущем году предприятие производит до 300-400 тонн сырья в месяц, поставляя около 70% готовой продукции на экспорт. Завод построен по самым современным стандартам, в том числе экологическим. Специалисты и руководители предприятия рассказали и показали, как шкуры сибирских животных превращаются в кожу, из которой шьют первоклассную обувь в России, Китае, Монголии и других странах.
Этап первый. Прием сырья со всей Сибири
В Сибирском федеральном округе находится четверть сырьевого ресурса страны для производства кожи, рассказывает генеральный директор завода Сергей Филатов. При этом за Уралом нет ни одного предприятия, перерабатывающего шкуры КРС.
"Кожа является побочным продуктом, никто не выращивает скот ради шкуры. Мы принимаем любые. Наши основные поставщики — мясокомбинаты или бойни", – говорит руководитель производства завода Ольга Усова.
Собственно, первый цех — первичной обработки сырья. Шкуры здесь сначала отправляют на так называемый обессол — их помещают в огромный "дырявый" барабан и прогоняют по нему, избавляя от соли, грязи. Здесь же ставят клеймо, взвешивают.
И отправляют на сортировку — с помощью специального оборудования, в том числе на просвет, изучают каждую шкуру: ее толщину, качество, фиксируют недостатки, или пороки, как их здесь называют, — шрамы, зажившие язвочки, стертости и т. д.
"Оператор вносит данные в специальную программу, и она определяет, на какой поддон направляется шкура", – объясняет Валерий Киселев, мастер цеха первичной обработки сырья.
По его словам, в день обрабатывают от 20 до 25 тонн сырья. В цехе работают 22 человека.
Ни одна шкура или ее обрезь не выбрасывается. "Мы ничего не утилизируем. Вопрос только в том, куда мы направим сырье. Если шкура обладает хорошими свойствами, имеет мало пороков — прижизненных, съема или хранения, – мы ее направляем собственно на производство кожи. Если пороков много, шкура идет на изготовление белковых продуктов — их используют в производстве кормов для животных, биодобавок к ним. Это не наш профиль работы, но мы сотрудничаем с такими производствами", – рассказывает Ольга Усова.
Сейчас завод работает только со шкурами КРС. Но при необходимости предприятие могло бы перерабатывать свиную кожу, овчину и т. д.
Этап второй. Хром и зола
После первичной обработки шкуры отправляются на один из важнейших этапов, в ходе которых они превращаются уже, собственно, в кожу. Или, как говорят на предприятии, – в гольё.
Правильно этот процесс называется — отмокозоления. Визуально он напоминает процесс стирки в машине. Вот только в один барабан вмещается до 7 тонн шкур, таких барабанов несколько и процедура занимает до двух суток непрерывно.
В такие барабаны добавляются специальные химические материалы, с помощью которых шкуры промываются, из них вымывается соль, а затем удаляется волосяной покров.
Весь процесс максимально автоматизирован. На заводе установлено исключительно европейское оборудование — в основном итальянское, но есть немецкое и швейцарское, рассказывает Ольга Усова.
Подача воды, значительного объема химматериалов производится в автоматическом режиме.
"Задается обработка с разными режимами для каждого барабана. Фиксируется каждый этап процесса, вплоть до считывания штрихкодов с упаковок с химматериалами", – разъясняет Сергей Низовский, ведущий технолог завода. – Все сливы также происходят автоматически — на собственные очистные сооружения.
"Там, где могло бы работать пять человек, у нас работает один", – говорит эскперт.
Затем — в других барабанах производится так называемое дубление кожи с помощью солей хрома. Кожа выдерживает высокую температуру — свыше 100 градусов, благодаря чему затем не дает усадку.
После этого кожа отжимается и поступает на следующий этап.
Этап третий. Двоильный
Изделие поступает в цех обработки краста. Краст — это кожа без так называемой лицевой отделки, которая наносится в самый последний момент, уже на специализированном оборудовании. Из самого краста, впрочем, тоже делают обувь, например, берцы. Алтайское предприятие, специализирующееся на этом, уже закупает в Заринске кожу.
Именно с этого цеха начинается изготовление самого краста. Двоильно-ленточная машина разделяет полуфабрикат, то есть все полотно поступившей кожи животного, повдоль (!) на две части, то есть как бы на два тонких пласта менее 1 мм каждый, рассказывает Алексей Гориленко, мастер цеха.
Для этого создается определенная влажность кожи — 53-58%. Если она будет более мокрой, нож "поплывет", если более сухой — разрез также будет неровным, а это — брак.
Верхний из полученных слоев — лицевой, самый лучший. Нижний называется "спилок". Он обладает ничуть не худшими качествами, но его поверхность более шершавая. Кстати, именно из него производят подавляющее большинство обуви, которую в магазине представляют как замшу.
Отсюда краст поступает уже в красильно-жировальные барабаны, где приобретает определенный цвет, чаще всего черный, однако технологии позволяют задать и другой оттенок.
Этап четвертый. Сушка
Просушивают кожу тоже в несколько этапов. Сначала ее — при определенной влажности — растягивают на специальном оборудовании в четыре-пять приемов, объясняет Светлана Фирсова, мастер участка. Это нужно для придания коже эластичности.
Затем происходит вакуумная сушка, в ходе которой коже также придают определенную форму. Затем — черёд атмосферной сушки: кожу помещают на специальный конвейер. Затем уже готовый краст "пролёживается" около 6 часов. Окончательная влажность – 12-14%.
Уже потом коже придают мягкость, проводят контрольное измерение. Все — краст готов.
Незаменимые свойства
Кожа — уникальный продукт, уверена Ольга Усова. За счет своей структуры она "дышит", сохраняет тепло, пропускает наружу пар, но не дает попадать влаге внутрь.
"У кожи высокие износостойкие свойства. Она устойчива к перепадам температур. Обладает мягкостью и способна принимать форму тела. Только натуральная кожа может сесть по ноге. Никакая искусственная такими свойства не обладает", – уверена эксперт.
Кожа может быть лаковой, велюровой, ей можно придать любой цвет и нанести на нее любой рисунок с помощью специальных технологий.
Кто покупает кожу
По словам генерального директора, предприятие ориентировано главным образом на рынок Юго-Восточной Азии. Именно с расчетом на это направление головное предприятие "Русской кожи" в Рязани принимало решение о размещении завода в Заринске.
"Логистически предприятие построено очень выгодно. Мы получили сокращение времени доставки кожи до конечного потребителя до трех раз. Наши основные потребители — Китай, Монголия, возможно, Индия, – рассказывает Сергей Филатов. – В основном наши покупатели — обувные фабрики. Рынок обуви только в Китае огромен, там производится до 1 млрд пар в год".
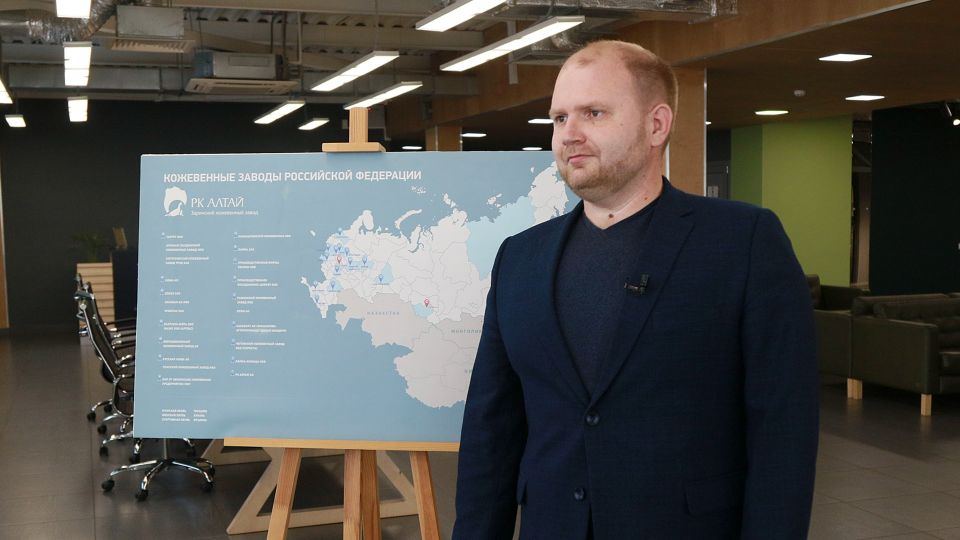
Он отметил, что запуск завода практически совпал с началом пандемии: "Многие заводы в Азии закрылись или приостановили работу. В связи с этим мы вынуждены были отправлять свою продукцию на головной завод. Но в 2021 году ситуация значительно улучшилась, и на сегодня 70% продукции отправляется в Китай. Этот год мы прошли на уровне 50%-ой загрузки. В 2022 году планируем достичь уже 90%".
Между тем, отмечает Филатов, на предприятии надеются на развитие сопутствующих кожевенных производств вокруг заринского предприятия. Опыт Рязани показывает, что это выгодно всем участникам процесса:
"Вокруг рязанского завода образовался кожевенный кластер — более 1 тыс. предприятий, от самозанятых до крупных производств. У них есть доступ к дешевой сырьевой базе — коже. В этих условия можно легко конкурировать с продукцией, выпускаемой в том же Китае", – объясняет Филатов.
Высокая экологичность
Предприятие в Заринске изначально строилось с учетом самых высоких экологических стандартов. Около трети стоимости самого строительства составили инвестиции в создание собственных очистных сооружений.
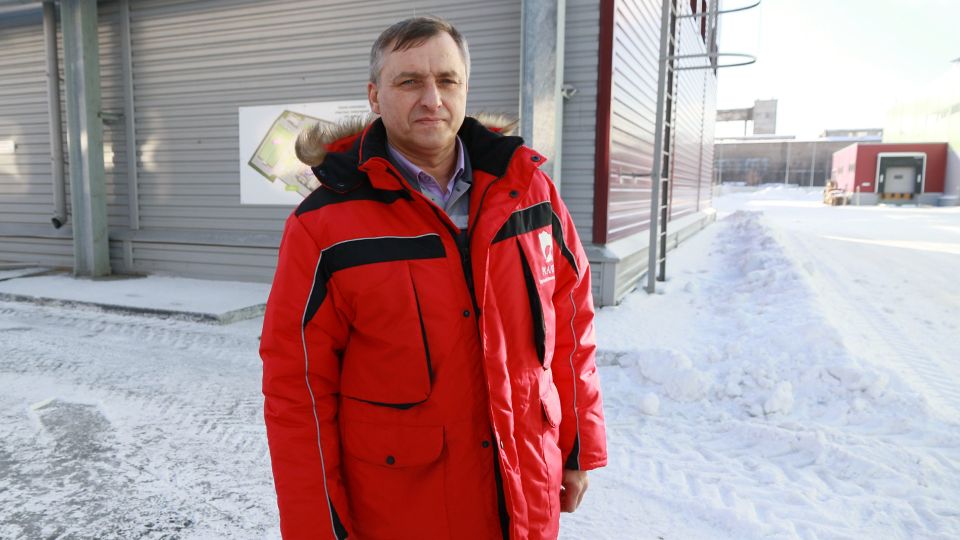
Общий объем переработки на них доходит до 800 кубометров в сутки, рассказал Вячеслав Постнов, ведущий инженер-механик предприятия. Очистка вод осуществляется отдельно по нескольким стокам — с этапа золения, дубления, мездрения и — отдельно — бытовых отходов.
"Зольные и хромовые стоки поступают на систему рекуперации — после специальной очистки по замкнутому циклу вновь поступают на производство. Это позволяет экономить до 7% воды и, соответственно, и затраты", – говорит эксперт.
Также очищаются все воздушные массы перед тем, как выбрасываться в атмосферу. "То есть мы минимизируем выбросы полностью", – говорит ведущий инженер.